The International Longshoremen’s Association reached a deal to discontinue their strike until January 15, 2025
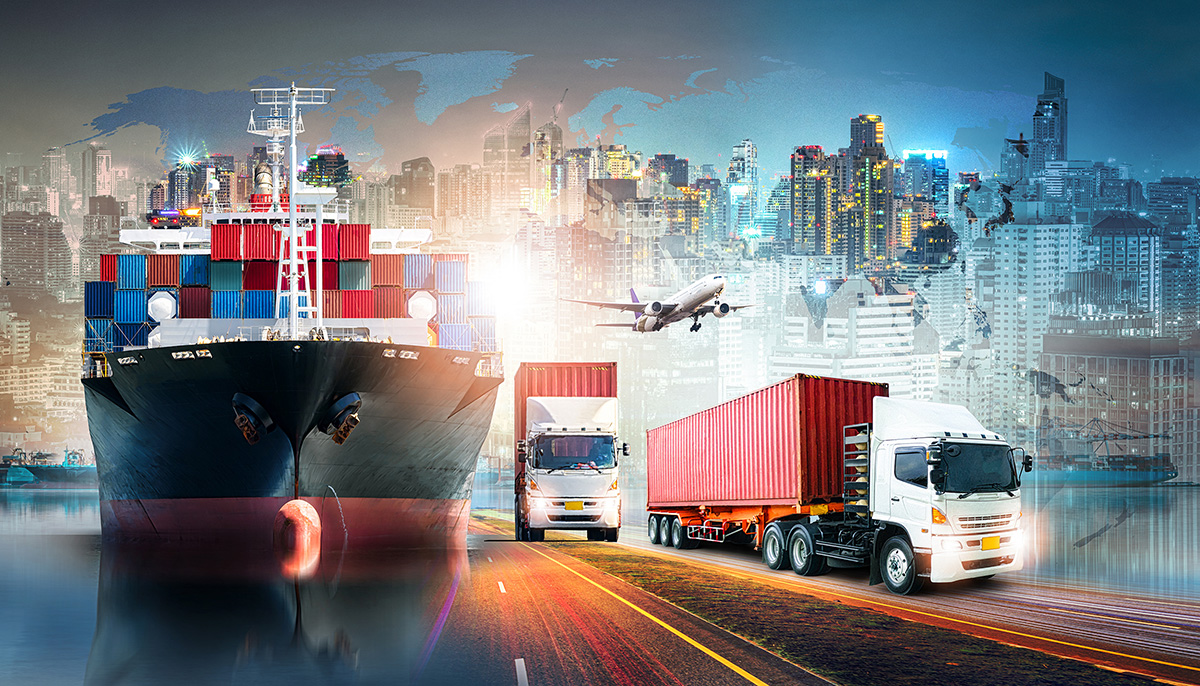
On October 3, 2024, the International Longshoremen’s Association reached a deal to discontinue their strike until January 15, 2025. This strike would have affected ports along the East and Gulf coasts causing disruptions in the supply chain for all industries. Industry analysts stated that for every day of a port strike, it takes four to six days to recover. What if there is no deal reached in January? Now is when you need to prepare for the impact to your supply chain.
Companies are looking at several strategies to avoid supply chain disruptions: increasing inventory, safety stock, alternate transportation, strength suppliers’ relationships, and alternate suppliers (local versus offshore). These strategies require visibility into their supply chain with more timely and accurate information.
Look at how you are acquiring this information today. Are you utilizing manual processes? If so, they are plagued with errors and delays. Examples of these delays and errors are:
- Human Errors – typos and mis-keyed information.
- Process Inconsistency – Different employees may follow procedures differently.
- Delays and Bottlenecks – If one person in the process is unavailable, the tasks might stall until they are available again. If there is a large volume, the process takes more time.
- Traceability – Without automated logging, it is hard to identify who made the change, when and why.
- Data Integrity – Manually entering the same data into multiple systems increases the risk of duplicates and errors.
- Rework – mistakes require rework, slowing down the processes.
- Loss of Information – Paper-based documents can be lost, damaged, or misplaced.
The best place to start to automate manual and error-prone tasks is where there is the largest volume of manual tasks involved in completing the process. Most companies are very proficient in automating their processes with their customers. However, if there is a dock strike, it will impact your suppliers and transportation options. Automating these processes through implementing Electronic Data Interchange (EDI) with them is a great place to begin. Most transportation companies have advanced processes utilizing EDI. If you are reevaluating your supplier base, this is a great time to implement suppliers with electronic document processes. Receiving timely and accurate information from your suppliers and logistic companies will allow you to increase inventory, have safety stock, implement alternate suppliers and gain more visibility into your supply chain to prepare for a dock strike or other disruptions in the supply chain.
Click here to learn more about Innovate Managed Services and Innovate’s Supplier Toolkit info@innovateec.com